Instrument Repairer, Clingan Guitar Tone
Program: Certificate IV in Instrument Making & Repair
It all started when I worked in a guitar store in NSW. Being a drummer, I was actually employed to sell drum sets, but the owner of the business, Phil Haworth, was a very well respected guitar maker and repairer and I would always find myself hanging around the repairs bench and not in the drum department. I think I must have annoyed him that much that he asked me to help out with the easy stuff and it went from there. I haven’t sold a drum set since.
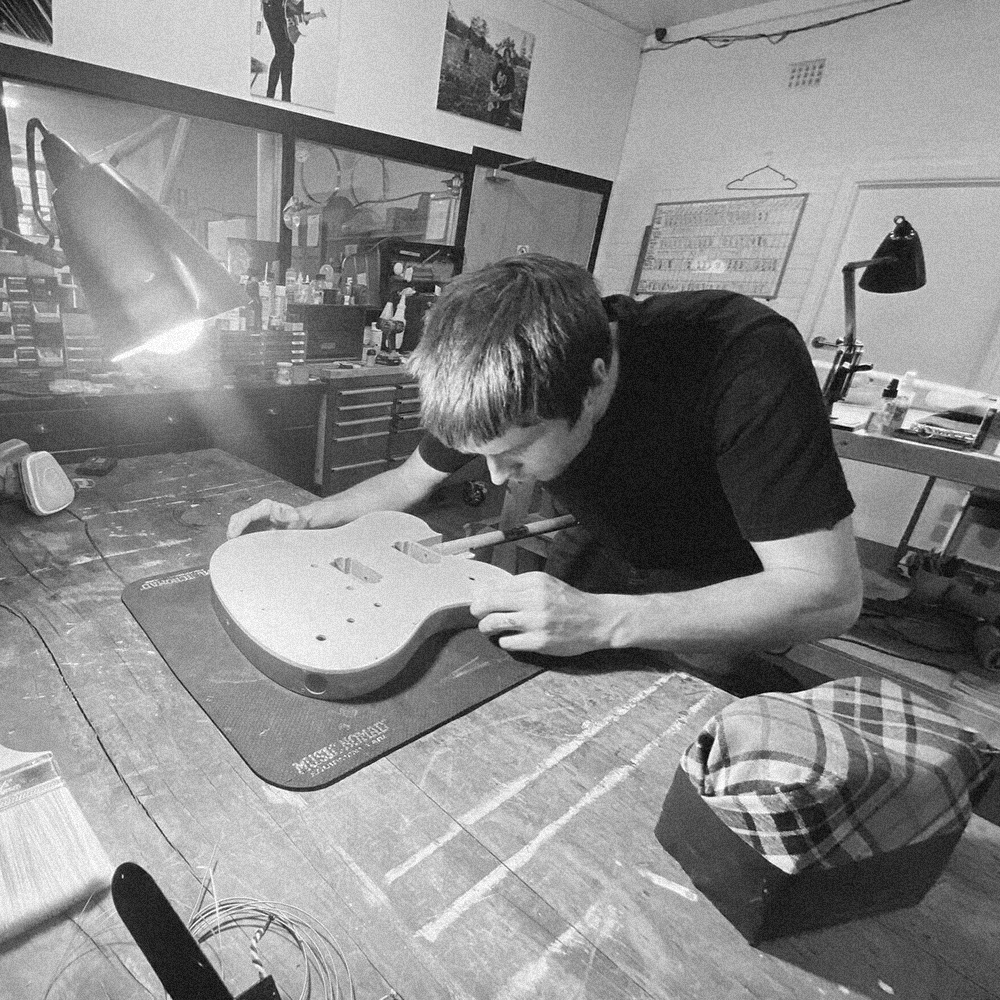
Follow
How long have you been Guitar Making and what related studies have you completed?
I have only been building for 18 months or so. I moved from Sydney to Melbourne to study and started my own little business on the 1st of November last year. NCAT was the College at which I studied the Cert IV in Instrument Making & Repair. It was a ten month course that provided me with the background knowledge and a chance to build 3 guitars.
What’s your business?
My business is T Guitars. I build electric 6 string guitars and 4 and 5 string basses.
How would you best describe your building style and your guitar’s aesthetics and sound?
My building style is ‘No Bull’. Not exotic, boutique or “custom”. I’m not one for caring about rare tone woods from the deepest Amazonian tundra or timber cut from a log found locked in an Icelandic glacier for 4000 years. Not me. I want the guitars I build to look, feel and sound great and I believe the shape of a scratch plate can do more for the overall aesthetic then if the tops quilted or not.
The first customer to order a guitar from me last year put it best. He said “In my collection of guitars I’ve got Les Paul’s, Tele’s, Strat’s, Ricky’s(Rickenbacker) P-Bass’s and more old guitars and this will definitely stand out. But it won’t look out of place”. And I’ll never forget that.
What’s the most rewarding part of making a guitar?
Going to a local gig and seeing one of your guitars being played. You can’t beat that feeling! I’m getting some noted players interested in my builds and am getting some really positive feedback.
What advice would you give to someone considering a career in Guitar Making?
You could create an account on any Guitar Makers Forum and see how that goes…Or go and have chat with an actual builder and see what it’s all about, because I’ve only ever found them to be friendly and happy to share their knowledge. But either way, do it! It’s good fun. There is a Guitar Expo on at Fed Square on Sat 29th Nov with plenty of friendly makers who are interested in talking about instrument construction.
Where can people learn guitar making skills?
There are plenty of Luthier run courses around the country where you spent a number of weeks building individual instruments. They’re pretty popular.
NCAT (Preston) run a full time Certificate IV course -the only place where students can gain a nationally recognized qualification- and there is also the option of a one day a week program where students can either gain experience or complete a Certificate III.
After building their instruments, student can graduate with an Electric, a Dreadnaught acoustic, and a custom designed guitar of their choice to take away.
Guitar building facilities available for learning and production?
The facilities at NCAT are second to none. The college has a $17M Technology centre, filled with high-end machinery including, CNC routers Multi Cam flatbed router, and a number of laser machines. All of this sits alongside traditional wood-working and guitar making equipment.
With all of this equipment it gives students the opportunity to gain exposure to traditional instrument maker hand working skills right through to the latest mass production methods of guitar making.
Who are the teachers for this course and are there any guest lecturers involved?
We were very lucky at NCAT Instrument Making to have years of professional experience on our side. Bon Nardella is the program manager, who apart from a successful music career in production and performance brings many year of expertise in instrument repair & set up.
As well as the full time staff having a wealth of experience, NCAT also brings in a variety of guest lecturers and practitioners. Over the last few years Ian Noyce, Jack Spira, Benedict Stewart, Andy Allen & Patrick Evans (Maton), have all been involved in either advisory roles as industry experts.